Don’t Let Your Essential Technology & Staff Freeze Up! 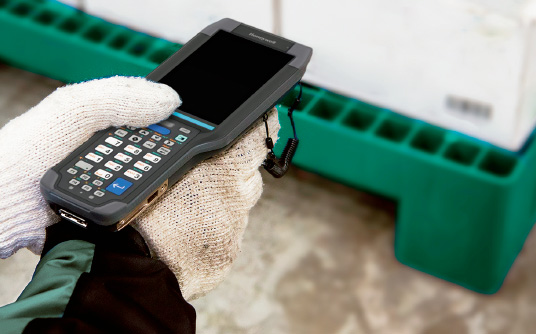
Cold storage, refrigeration units, and freezer units often create challenges to ordinary wireless computers. The changes in temperature from freezer to loading dock can create condensation which causes computer screens to fog up, keyboards to seize up, and internal parts to corrode. Make sure you’re using the right devices for cold storage scanning.
Contact Our Technology Experts
Standard Device Challenges in Cold Storage Applications
Companies no longer have to compromise on functionality and information access just because of their environment. Devices built for cold storage scanning are able to withstand the cold temperature as well as the transition from cold to warm locations. Cold air, frost, and condensation all create challenges when it comes to cold storage scanning equipment.
- Fogging of the scan window – when the scan window fogs, the scanner is no longer able to “see” the barcode which prevents scanning.
- Fogging of the display – internal condensation fogs the display and users can no longer read the screen.
- Reduced display refresh rate – cold temperatures reduce screen refresh rate and when screens refresh slowly, users spend time waiting instead of on task.
- External condensation – when users leave the cold storage units, condensation can drip onto the keyboard area or display. When re-entering the cold temperatures, condensation can freeze or cause frost build-up, making it close to impossible to enter or retrieve needed data.
- Reduced battery cycle times – users need to swap standard batteries need more frequently during a shift when used in colder environments. This impacts productivity and capital costs.
- Internal condensation – condensation that forms and remains present inside the device will cause major damage over time. This ultimately results in increased repair requirements.
Using devices designed for cold storage environments will help streamline cold storage handling, increase accuracy and productivity, and help reduce errors.
Industry Guide: The Cold Hard Facts of Using Rugged Mobile Computers
Use Voice-Assisted Picking For a Total Solution
Although your mobile devices are important, your staff is even more essential. So make sure they stay warm even in the coldest storage units. One solution that many cold storage facilities have found successful is the use of voice technology. Adding voice to devices is easy. And, companies that start using voice enablement start seeing the benefits in just a few weeks. Using voice as part of multimodal data capture speeds has several benefits:
- Avoid numb fingers: Voice is part of a multimodal data capture solution. However, gloved hands and harsh environments mean any time data can be collected automatically, you’re working faster. You don’t want workers fumbling with keyed data entry while shivering.
- Keep moving, stay warm: Watch your workers. When they read their device screen or enter data, their feet stop moving. With voice, workers are entering data while moving, saving your business time, and getting them out of the freezer faster.
- Works with Freezer mobility: voice software works with your preferred freezer-rated mobile computer – whether it’s forklift-mounted or handheld. Couple the device with a freezer-rated rugged headset, and you’re ready.
- Put development costs on ice: voice-enable your existing telnet or browser-based mobile application and easily integrates with Andriod mobile computers.