Trek Bicycle Maneuvers Through Device Management Challenges and Downtime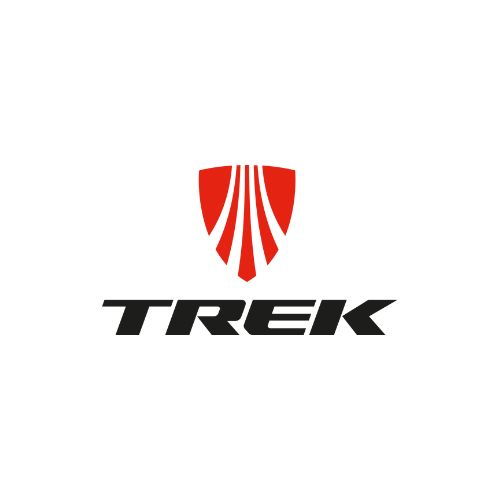
Founded in a small Wisconsin barn in 1976, Trek Bicycle has been determined to create the highest quality bikes and bring forth meaningful joy in cycling for all. From a humble beginning, President, John Burke, and his father created something special for cyclists. The company offers a variety of bikes and apparel to suit customer needs, rooted in the unique idea of offering something different to the cycling community. Trek has offices around the world, 6 warehouses across the US and Europe, and does business in over 80 countries.
The Challenge:
Trek employs hundreds of staff members at its distribution and manufacturing facilities in North America and Europe. Many of whom use mobile handheld devices and barcode scanners across multiple shifts to track inventory, assets, parts, and shipments throughout Trek’s manufacturing operations and supply chain. The IT team responsible for managing Trek’s data collection platforms and process were struggling to efficiently troubleshoot hardware issues, perform security updates, and proactively monitor the overall health of these devices. The team also lacked visibility on where their devices were and who was using them on a given shift.
Trek is deeply committed to the success of its retailers and the cycling community. If a retailer places an order by 5 pm, Trek’s distribution facilities will still ship the order out that same day to ensure stores have stock and cyclists can enjoy their next ride. To meet those commitments, the Trek team could not afford the downtime they were experiencing with their device troubleshooting processes. IT staff would often drive several hours to different facilities to fix or patch devices or inefficiently troubleshoot over Microsoft Teams messages without the ability to directly log into a device to diagnose and fix a problem.
With a boom in bicycle demand during the pandemic and big weekend sales, Trek needed to become more efficient and connected so they could continue providing the best possible experience for their retailers and riders.
The Solution:
Trek collaborated with their long-time technology provider, RMS Omega Technologies, to evaluate enterprise mobility management tools from SOTI. RMS Omega and Trek have been working together since 2003 to deploy various data collection technology solutions throughout Trek’s supply chain, including enterprise mobile and wearable devices, barcode scanning systems, thermal printers, labels, and printing supplies. The RMS team recommended the SOTI One Platform, specifically SOTI MobiControl and SOTI XSight to ease Trek’s challenges and better support their fleet of mobile devices.
Starting with a proof of concept on 32 devices, it was clear that SOTI’s MobiControl application would easily simplify their current processes to locate, manage and monitor their fleet and seamlessly roll out necessary updates and security patches when needed. Furthermore, SOTI XSight quickly simplified the help desk team’s abilities to proactively monitor device performance, provide fast user support when help is needed and ultimately prevent downtime.
The Results:
SOTI MobiControl and SOTI XSight have improved operational and worker efficiencies to support surging production and shipping demands, allowing Trek to keep their bikes, parts, and accessories in stock and ready for the next cyclist. With the help of RMS Omega and SOTI, Trek improved device visibility and can now monitor how, when and where their devices are being used. With SOTI MobiControl, IT staff can easily set up and configure a device by dragging and dropping a folder in the system. Different profiles are deployed for workers’ roles and locations to ensure the scanners and handhelds are set up correctly for each task throughout their operations.
With SOTI XSight, Trek’s IT team can quickly diagnose, support, and troubleshoot issues without physically being at the same location as the user or going back and forth over Microsoft Teams or phone calls and text messages. They can instantly remote into the device and see exactly what the user is seeing, expediting helpdesk issues, and keeping their technology working as intended. The platform has also helped new, and temporary workers get up to speed quickly, saving valuable onboarding time.
“We would spend hours throughout the week supporting and updating devices. Now with SOTI MobiControl and SOTI XSight, it’s down to minutes,” said Tom Spoke, Director of Global IT at Trek Bicycle. “It’s also safe to say we’re seeing a 15-20% time savings on new employee onboarding.”
And thanks to their new capabilities, Trek’s team members are better equipped for the busy Monday rush. “Before using SOTI MobiControl, if 10 workers had a problem with their devices at the end of the day, and it took at least 10 minutes to solve each problem, that could be 100 orders that don’t get out the door that day and that’s a problem. Using the SOTI platform, we can quickly solve and prevent those issues to limit the amount of stoppage time for our warehouse staff,” said Spoke.
“We are thrilled to support our long-time customer, Trek, with a better way to manage their devices,” said Peter Vatenos, VP of Marketing & Principal at RMS Omega. ““The SOTI MobiControl and SOTI XSight implementation has helped reduce downtime, and we are pleased to see its positive impact on Trek’s operations so far. We look forward to continuing to support our longtime customer and their future technology advancements.”
Learn More About Trek’s Commitment to the Community
Learn more about Trek, their initiatives, and the communities they support. Want to ride today? Trek can help you find the perfect bike for the road, trail, mountain, or whatever path you choose.
Contact RMS for Help With Your Next Project!
Get started with a solid device management solution – RMS Omega’s solutions experts can help you evaluate, design, and deploy a system to meet your demands.